The Fight for the “Right to Repair”
Manufacturers have made it increasingly difficult for individuals or independent repair people to fix electronics. A growing movement is fighting back
/https://tf-cmsv2-smithsonianmag-media.s3.amazonaws.com/filer/65/bf/65bffceb-cf05-4976-9ff1-0f9157a23bec/camera-repair.jpg)
Fifty years ago, if your television broke you could bring it to the local electronics shop to be repaired. These days, a broken TV likely means a trip to Best Buy for a new one.
Electronics have become harder to fix. This is, in part, because they’ve become more complex. But some of the problem is by design. Manufacturers have increasingly restricted repair information to authorized repair centers, leaving consumers and independent repair people unable to deal with even simple problems. It's just easier (and sometimes cheaper) to buy something new.
A growing number of people, seeing this as an unreasonable state of affairs, are fighting back. In a so-called “right to repair” movement, this loose coalition of consumer advocates, repair professionals and ordinary individuals are working to create legislation that would make it harder for companies to keep repair information proprietary.
The idea of planned obsolescence is nothing new. But the use of “repair prevention” as a method of making products obsolete is growing, say right to repair proponents. Many companies that manufacture electronics—anything from laptops to refrigerators to your car’s onboard computer—now have restrictions that prevent consumers from having them fixed anywhere besides a licensed repair shop. Some companies use digital locks or copyrighted software to prevent consumers or independent repair people from making changes. Others simply refuse to share their repair manuals. Some add fine print clauses to their user agreements so customers (often unwittingly) promise not to fix their own products.
“Most people experience the problem, but they have no idea that’s there’s a solution, and they have no idea that the manufacturers are behaving badly,” says Gay Gordon-Byrne, the executive director of The Repair Association.
Gordon-Byrne’s organization, a nonprofit that lobbies for right to repair laws, was founded three years ago. Over the past year, the group has started to introduce legislation at the state level. They currently have about 180 official members, many of them large organizations such as repair professional trade associations or environmental advocacy agencies.
iFixit, a website that provides repair instructions and DIY advice and tools, approaches the problem from a different angle: if companies won’t provide us with the information to fix our own products, we’ll figure it out ourselves. The site functions as a sort of repair Wiki, with some one million users sharing knowledge. Its CEO, Kyle Wiens, came to the right to repair movement after working as a technician at an authorized Apple repair center.
“I knew what authorized technicians had access to,” he says. “Then, when I was at university, I was trying to repair my own laptop and I looked online and couldn’t find any information. It’s kind of inevitable that, as a manufacturer, you want to control everything. But that’s not what’s best for consumers.”
The problem, Gordon-Byrne says, began in earnest in the late 1990s. Companies were increasingly embedding software in their products, and claiming that software as their intellectual property. Companies would argue that they needed to control repairs as a way of maintaining security and customer experience, reasons Gordon-Byrne calls “all fake.”
“Look at all the stuff you own that has a chip in it,” says Gordon-Byrne. “I looked around my home and I counted 29 before I left my driveway. It’s in every clock, every TV, everything that’s connected to the internet. I have a bathtub that has a whirlpool feature that’s controlled by a circuit board that no longer works. You can’t get away from the chips, and if you can’t fix them you’re really going to have to replace [the product].”
The problem isn’t limited to traditional home electronics. A farmer may have paid for his or her John Deere tractor, a piece of farm equipment that can run in the hundreds of thousands of dollars. But John Deere still owns the software that runs the tractor, and trying to fix it without going to an authorized repair center could put the farmer afoul of copyright laws. This means that, in order to make legal repairs, a farmer in a rural area might have to haul a broken 15-ton tractor for hundreds of miles to an authorized dealer or repair shop. In the harvest season, this could mean a crushing loss of revenue.
Nor does the problem only harm consumers. Independent repair professionals, from camera shop owners to computer technicians, suffer, saying the lack of access to repair parts and manuals makes them unable to do their jobs.
Companies have a two-part incentive to make their products difficult to repair. First, if they control repairs, they can make money off of them. This benefit is increased by the fact that a company that monopolizes repairs can set higher prices than the market would otherwise bear. An authorized iPhone battery replacement for an out-of-warranty phone costs $79. The unauthorized iPhone battery replacement I had done in a Hong Kong electronics mall, where there’s plenty of competition, cost me about $30. A DIY iPhone battery repair kit from iFixit costs $34.95.
When Gordon-Byrne’s Subzero refrigerator began having problems “366 days” into a one-year warranty, she went looking for an independent repair person to fix it. But Subzero, she soon discovered, didn’t sell parts to non-authorized repair people. The minimum price for hiring a Subzero repair person was $300, she says.
A product that has software embedded in its design is even more difficult to repair, since you can’t simply replace a part with a similar one. When consumers do create workarounds to allow themselves to repair their own items, some companies fight back.
Earlier this year, many iPhone 6 owners found themselves with nonworking phones after an Apple iOS update detected that they had had repairs done at an unauthorized shop. Without warning, the update put their phones on permanent, unfixable lockdown. (After a public outcry, Apple apologized and offered a fix to the problem, saying it was meant as an in-factory security test and not intended to affect customers.) A self-cleaning cat litter box called CatGenie had a “SmartCartridge” of cleaning solution that stopped working once it was opened and refilled a certain number of times. The owner was then forced to buy a new SmartCartridge from the company. It’s since spawned a thriving market in devices like the CartridgeGenius cartridge emulator to outwit this mechanism.
Companies that see their products being altered or repaired without authorization have often taken legal action. In 2011, Apple sued a New York teenager for trademark infringement after the 17-year-old sold kits to convert black-colored iPhones to white-colored ones, using cases he’d purchased directly from the supplier in China.
The inability to self-repair ones possessions is an even more urgent problem in the developing world and among disadvantaged populations. Wiens tells the story of an independent medical device repair technician in Tanzania who has a website where he shares information on fixing medical equipment such as infant incubators, cardiac monitors and autoclaves.
“He gets legal friction from medical manufacturers all the time,” Wiens says.
But in countries like Tanzania, using an authorized repair outlet may not even be an option.
“Is Medtronic going to send a repair technician to a hospital in Tanzania?” Wiens asks. “I don’t think so.”
In Minneapolis, a nonprofit called Tech Dump provides electronic recycling and refurbishment, employing workers not considered traditionally employable, many of whom have criminal records. The low prices of the organization's refurbished items allow people who might not be able to afford, say, a new computer purchase a good-condition laptop.
“They do a tremendous service for the community,” Wiens says, of Tech Dump.
But the company is having an increasingly difficult time with the refurbishment part of its mission. The company takes in some 5 million pounds of electronics every year, everything from cell phones to computers to TVs. But they’re only able to repair about 15 percent of these items, often because they can’t access repair information or proprietary parts.
“[Manufacturers] don’t have any repairs or any repair manuals available for purchase,” says Amanda LaGrange, Tech Dump’s CEO. “We’re not expecting them to provide items for free. We would absolutely purchase them because it would make us far more efficient.”
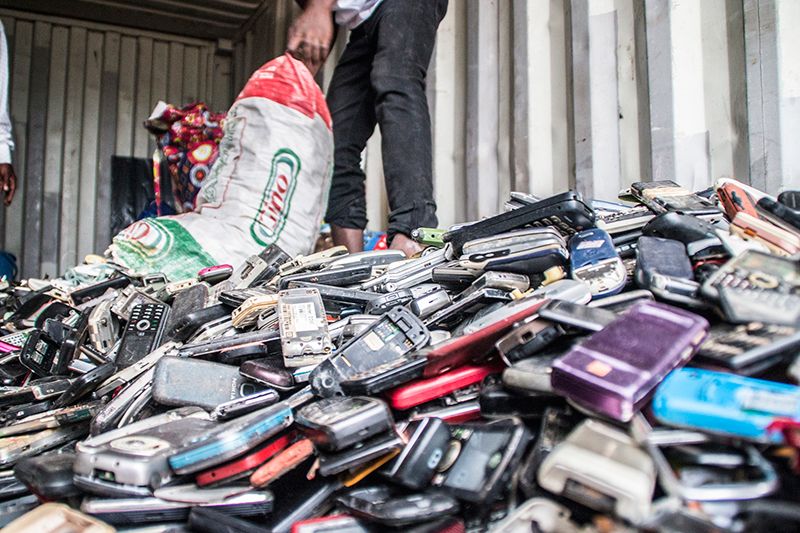
Related to all this is the growing problem of e-waste. The inability to repair a product shortens its lifespan and adds to the number of electronics winding up in landfills. A recent study by the German Environment Agency shows that the lifespan of home electronics is getting shorter. Some of this is due to consumers’ yearning for new, better products—about a third of purchases of “white goods” (major appliances like fridges and washing machines) were due to customer desire for an upgrade. But much of this has to do with items being faulty and—presumably—difficult to repair. The percent of white goods being replaced within five years because of “technical defects” increased from 3.5 percent in 2004 to 8.3 percent in 2012.
According to research from the UN, the world produced about 41.8 million metric tons of e-waste in 2014. Only a fraction of this—about 6.5 million metric tons—was recycled through government take-back programs. The amount of global e-waste is expected to increase to 50 million metric tons by 2018. E-waste is often highly toxic, leaching heavy metals and dangerous chemicals into the soil around landfills and releasing greenhouse gas and mercury emissions when burned.
“If we all just used our electronics for longer, it would definitely decrease the environmental impact,” LaGrange says.
When I first reached Gordon-Byrne, she told me I was catching her in a “moment of great frustration.” The Repair Association had introduced “Fair Repair” bills in four states—Massachusetts, Minnesota, Nebraska and New York. These bills called for manufacturers to provide “fair access” to service information and replacement parts for owners and independent repair people. But by last month, it was clear that none of them were going to progress, dying in committee or when the legislative session ended. Right to repair advocates blame the manufacturers. Apple, for example, was found to have funded lobbying efforts to kill the Fair Repair bill in New York.
Gordon-Byrne says she’s still hopeful similar bills will pass in upcoming sessions. She and other right to repair advocates take inspiration from recent events in the automotive industry. In 2012, Massachusetts passed a bill forcing car manufacturers to provide independent repair shops with the same diagnostic tools they give authorized repairers. In 2014, the automotive industry, seeing that other states would likely pass similar legislation, agreed to make the same data available nationwide by 2018.
If Fair Repair bills begin passing in select states, right to repair advocates hope it will cause a similar sea change in the electronics industry.
“The manufacturers are not going to be able to keep this up forever,” Wiens says. “It’s just a matter of time.”