Can This Trash Can Turn Food Waste Into Garden Treasure?
The Zera Food Recycler may not transform scraps into ready-to-use soil, but it could still help take a bite out of landfill-bound waste
/https://tf-cmsv2-smithsonianmag-media.s3.amazonaws.com/filer/a2/b8/a2b8bbc5-80ec-4263-950c-5fa95f69d40f/zera-food-recycler.jpg)
There are many parts of produce that consumers don’t usually eat—apple cores, orange peels, carrot tops, cucumber butts. That’s not to say that inventive chefs haven’t found ways to use these commonly trashed edibles. But in most developed nations, people waste a lot of food.
To put this into perspective: Every year, roughly one third, or 1.3 billion tonnes, of food produced worldwide for human consumption is wasted, according to the United Nations Food and Agriculture Organization. While a similar amount of food is wasted in both industrialized and developing countries, in the former regions, a whopping 40 percent of the waste can be pinned on consumers and retail.
And that’s a big problem.
Aside from the many people this waste could feed, billions of pounds of food heads to the landfill each year where it sits, decomposing and producing methane, a potent greenhouse gas. But an innovative composting device, the Zera Food Recycler, hopes to take a bite out of this mounting food waste.
The Zera recycler is the brainchild of WLabs, Whirlpool’s innovation incubator. First conceived in 2012, the device is a little larger than a standard kitchen trash can and, with the help of an additive, can turn food scraps into something resembling fertilizer.
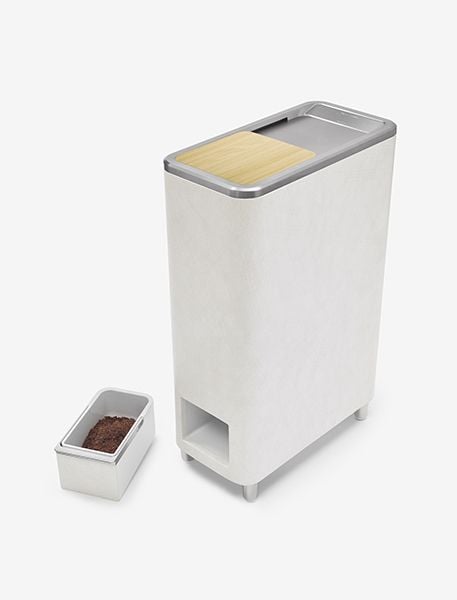
If executed correctly, composting is a win for the environment. No matter how you slice it, cucumber butts are always going to be an issue. But tossing them into landfill-bound trash can have more of an impact than most imagine. The piled trash has to be trucked to the nearest landfill (sometimes across state lines), where it produces enormous amounts of methane.
“If you put all the food waste into one country, it would be the world’s third largest greenhouse gas emitter,” Brian Lipinski, an associate in the World Resource Institute’s Food Program told Smithsonian.com in 2015.
Heaps upon heaps of trash are piled up in landfills, left to decompose with little aeration or stirring. This means that the trash undergoes what’s called anaerobic degradation—a process that emits methane, which heats the planet much more (up to 86 times) than its greenhouse gas cousin carbon dioxide. This type of anaerobic degradation can even happen in poorly tended compost piles that are not turned or otherwise aerated on a regular basis.
Even so, traditional composting can take months, requiring intense and prolonged microbial action to convert food to the earthy-smelling brown stuff you can liberally apply to lawns and gardens. And tending to the heap of degrading food—aerating the pile, adjusting the acidity, optimizing the carbon to nitrogen ratio—can only speed up the process so much.
So how does Zera deal with these limits? “It’s a really easy answer,” says Tony Gates, the project lead for Zera. “We’re doing no microbial breakdown at all.”
Zera relies on heating the material to start the decomposition—or rather liquefaction—process. According to the company’s website, throughout the week you can put all of your food waste (from fruit to veggies to meat to dairy, minus any large pits or bones) into the device and close the lid. When the machine is full, just drop in the additive pack—essentially, a combination of coconut husk and baking soda, says Gates. With a push of a button, the machine takes over, heating the soon-to-be food goo to a toasty 158 degrees Fahrenheit. A central auger slowly turns to agitate and aerate the mix and fans continually run to dry it down.
The squashed food transforms over the course of this process, which takes up to 24 hours—from liquified food to what’s known as the “peanut butter phase” to the solid phase to the loose fertilizer phase, says Gates.
The problem is what to do next, says Jean Bonhotal, director of the Cornell Waste Management Institute in Soil and Crop Sciences. “People have been working on these processes for a long time, and I love the idea of the process,” she says. “But [the resulting material] does have to be managed further.”
What comes out of the sleek device isn’t mature fertilizer, she explains. If you go out and sprinkle a hefty layer on your garden, not only would it start to smell as microbes get to work digesting the food, but it could also have negative effects on the health of your plants since the carbon and nitrogen are not yet in a form that greenery can gobble.
Gates agrees, but says that their tests suggest that a light sprinkling (with emphasis on light) of the material over plants can actually have positive effects after two to three weeks, as microbes mull over the rich material and release the nutrients into the soil.
“We’re letting nature do [the composting] after the fact,” says Gates. “But what we’ve done is we’ve sped up the process of decomposition to a point where nature can take what we give it and do it much quicker.”
But there are still a couple of concerns with this process, Bonhotal points out. First is the volume of the material that will be produced. “You’re not adding stuff to your plants 365 days a year,” she says. And the lightness of the sprinkle necessary to prevent stink and plant death will result in the pre-compost product building up overtime.
Though it can be stored in airtight containers for a year or more, says Gates, this is one of the kinks he and his team are still working out. One potential, he says, is to use the material as a starter or fodder for a backyard or community compost pile.
The second concern is for the energy requirements of the machine, says Bonhotal. Heating and turning both the auger and fans does consume energy. But, according to Gates, the company has done everything it can to make production and running environmentally sound—right down to the limited use of Styrofoam in the packaging.
“From the beginning we wanted to make sure it was very clear that there's a distinct advantage of doing this process over sending the waste to the landfill,” he says. But without lifecycle analyses of the device, it is difficult to tell if the product breaks even with emissions.
Though Zera Food Recycler still has some kinks to iron out, this sleek, $1,199 device could help in the bid to limit landfill-bound waste. So if you aren’t into carrot-top soup or misshapen-beet ketchup, Zera is an option. Just make sure you are ready to roll up your sleeves and tend to all that pulverized food.