Lasers Faster Than The Blink Of An Eye Could Change Glass On Our Phones
A new screen-chiseling method will give high-end finishes to low-end phones—and could revolutionize screens in everything from cars to smart watches, too.
/https://tf-cmsv2-smithsonianmag-media.s3.amazonaws.com/filer/5e/05/5e0598ae-d565-4607-a224-0de684ca7ee3/raydiance_r-cut_glass_perimeter_notch.jpg)
If you read gadget blogs with any regularity, odds are you see a new Apple rumor pretty much every day. Of late, one of the biggest—and most substantiated—is that the company will be using sapphire to create the screens for its next-generation iPhones.
Using a material like sapphire, however, is bad news for anyone who might have been hoping for a more affordable iPhone. Though the material is extremely scratch resistant, sapphire and other hard materials like it (including Corning’s popular Gorilla Glass) are extremely difficult to work with. Cutting and contouring these materials for smartphone screens is a delicate, multi-step machining process typically too time-intensive and costly for the mass market.
But today, the California-based company Raydiance is launching a new solution called R-Cut that claims to take care of all the work in a single pass. The secret: lasers. The system could allow high-end finishes to finally make it to middle- and low-end phones and tablets, including the long-storied $100 smartphone. But it could also revolutionize the quality and strength of glass we see in a range of other consumer products, from smart watches to in-dash displays in cars.
These types of lasers have been in university labs for years, but Raydiance is the first company to commercialize the technique in a way that allows it to integrate into existing manufacturing processes.
“There’s a lot of chopping and tracking when you try to cut with [conventional] tools, like a diamond-edged saw,” explains Michael Mielke, Raydiance’s chief scientist. “After the initial cutting, there are multiple steps involved in grinding and polishing the glass to smooth it out and remove the defects.”
R-Cut, on the other hand, is a complete glass shaping system. In it, a femtosecond laser delivers up to a quadrillion swift pulses of light each second—a rate about three times faster than the blink of an eye—to slice through materials. The technique enables manufacturers to removes little bits of material 100 nanometers wide, about as thin as a human hair. The speed and accuracy of the machine essentially “vaporizes” the material, Mielke says.
Before now, Raydiance’s laser cutting method was used for products less flashy than smartphones and tablets. The company’s first success was in medical devices: Their R-Tube and R-Mill systems are used to shape and cut cardiovascular implants, such as atrial valve replacements. And more recently, the company’s R-Drill has helped with automotive manufacturing by making precise holes in fuel injectors, helping deliver more gas to engines and improving fuel economy.
In phones and tablets, that kind of precision will initially be focused on manufacturing efficiency. Take an iPhone 5S, for example: The bezeled 45-degree edges around the perimeter of the screen, the speaker slot and the home button are painstaking to create and require multiple machines to complete. The R-Cut could do the same work in a single pass—an efficiency boost that could, ostensibly, pass some cost savings on to the consumer.
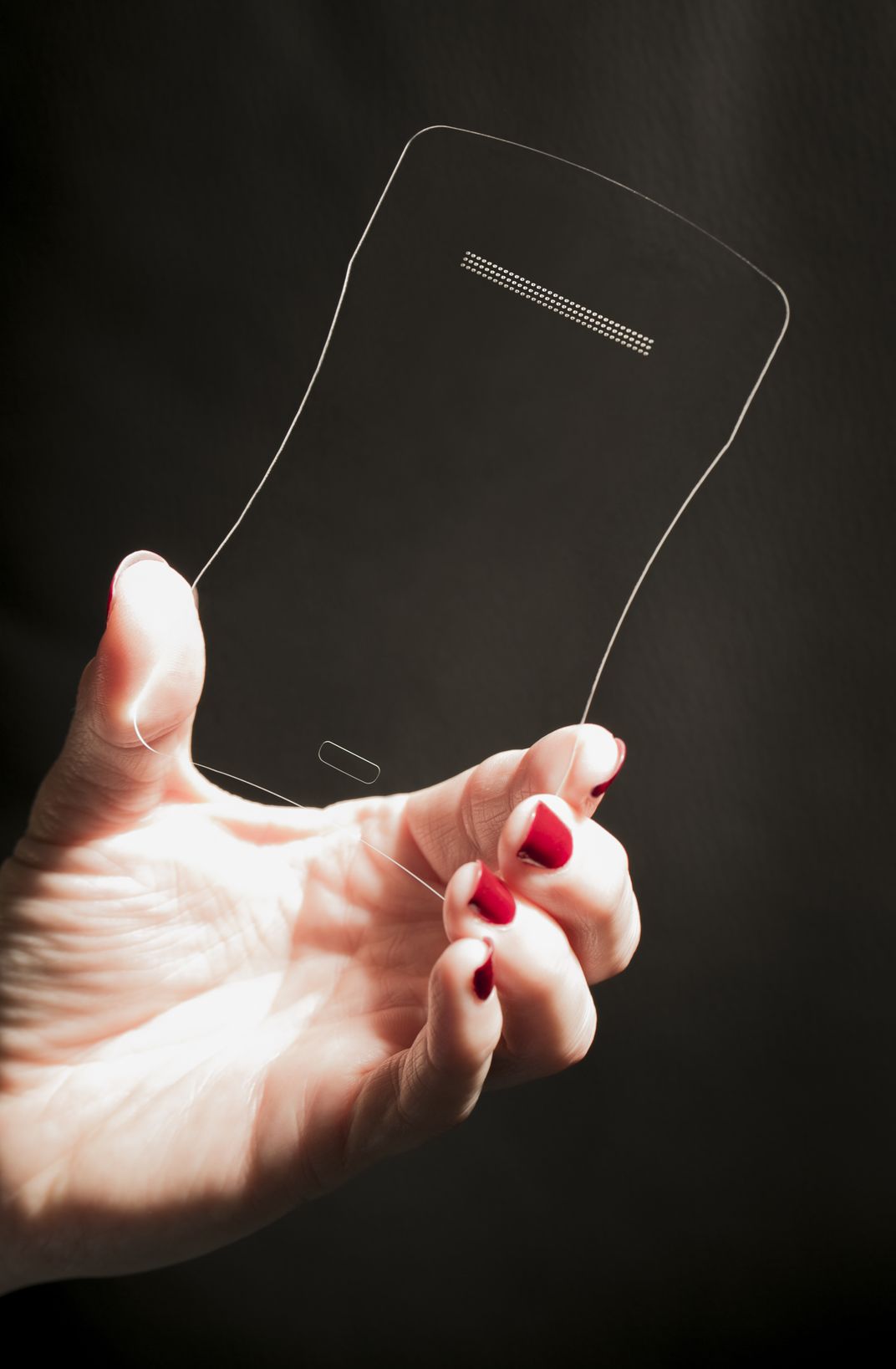
But eventually, the technology could also be leveraged to create new design aesthetics. Many concept phone designs have smooth, rounded edges—shapes that, with conventional cutting, would require 10 grinders and polishers, but that the R-Cut can handle on its own.
As we start to see more touchscreens in cars, a trend led by the Tesla Model S, laser-cutting could also be used to create luxurious, yet safe, in-dash displays. When conventional mechanical machining forms an edge, it creates microscopic stresses along the pane’s perimeter. Those imperfections—which, in theory, don't exist when using an R-Cut—can lead to cracks and fissures over time.
“The strength of glass is only as good as the quality of the edge,” warns Stefan Zschiegner, senior vice president of marketing at Raydiance. “If a crack starts at the edge, it will grow.”
Raydiance is the largest player in the world of industrialized femtosecond laser technology at the moment. The company has a working R-Cut system in place in a major smartphone factory, though it wouldn't say which one. Right now, the unnamed partner is using the system to rapidly prototype new phone models. But it won’t be be long before the sleek new displays make their debut, according to Zschiegner: we can expect to see phones with R-Cut contoured screens before the end of the year.