Elevators Are Going Green
Lifts are becoming more sustainable, as the percentage of the world’s population living in cities grows
/https://tf-cmsv2-smithsonianmag-media.s3.amazonaws.com/filer/60/c8/60c8f308-6d5f-47db-aac2-a4b23ec31227/schindler_7000.jpg)
Each day, more than seven billion elevator journeys are taken in tall buildings all over the globe. Considering that half the world’s population live in cities—a number expected to jump to 70 percent by the year 2050—efficient vertical transportation has become a pressing challenge. To keep pace with an influx of urban dwellers and rising sea levels, developers will not only need to build higher, they will also need to devise greener vertical transport: that is, safe and sustainable ways to move residents from the ground up into the sky.
Newer elevators already incorporate green features such as LED lights, water soluble paint and recycled construction materials, but many companies have begun to explore a wide and somewhat outlandish array of alternatives to the traditional rope-and-pulley systems of a hundred years ago. From diagonal travel (Las Vegas' Luxor hotel has an elevator that runs along its pyramid-shaped building at a 39-degree incline) to destination dispatch (grouping passengers bound for the same destinations into the same elevators) to something called magnetic motors (using a magnetic field to propel an elevator cab between floors), the world of vertical transport is one of high hopes and higher stakes.
We generally don’t give much thought to elevators, except during the brief moments we’re inside them. They may make us feel claustrophobic, awkward or impatient, but these vertical conveyances are in fact a marvel of engineering: not only do elevators shuttle passengers and freight up and down hundreds of stories—to hotel rooms and apartments, lobbies and basements—they also carry tons of steel cable each trip they make. The shafts in which they operate are essential to the structural integrity of a building, and their design can mean the critical difference between sustainable use of space and return on investment.
Unfortunately, many elevators in the United States rely on aging technology, clunky cabs and harmful lubricants, at significant environmental and financial cost. Consider that an elevator inside a typical skyscraper might weigh 80,000 pounds; hoisting all that mass requires a tremendous amount of energy. The taller the building, the more elevator shafts needed, each with their own motor; extra tall buildings often require a second sky lobby halfway between the ground floor and the roof. In fact, elevators typically account for between 2 percent and 10 percent of a building’s energy use. That includes materials—interior paints, carpet, control panels, lighting, ventilation systems—and the mechanical technology used to operate the cab itself.
Each of these elements contributes points to a building’s overall score for Leadership in Energy and Environmental Design (LEED) accreditation by the U.S. Green Building Council. Essentially, LEED is a globally recognized symbol of sustainability achievement, though many elevator manufacturers hire third parties to conduct lifecycle and toxicology studies on their materials. Buildings around the world are keen to get that seal of approval.
While LEED issued its most recent elevator standards in 2016, green vertical-transportation initiatives began as early as the 1990s. Machine-room-less (MRL) technology, for instance, eliminated the room that houses hydraulic oil and pumps—one of the biggest advances in elevator design since they went electric a century earlier. The room-less elevator consumes less vertical and horizontal space; without a machine room, a building’s flat roof can more easily accommodate expansive green areas with plantings and solar panels.
These days, manufacturers are chiefly interested in regenerative drive systems: elevators that recover some of the energy they consume. For the vertical transport industry, that means fostering an economy where sustainability is profitable. In 2017, Thyssenkrupp Elevator became the first company to retrofit an existing elevator to achieve net-zero energy. The project, which took place in Boston’s historical district, tested energy-generating cars that divert power back to the electrical grid. Engineers wanted to find ways to conserve energy when the elevator was running—and, more critically, when the elevator was not running.
“We’re actually producing more energy than we’re consuming,” says Brad Nemeth, vice president of sustainability at Thyssenkrupp Elevator Americas. A pioneer in vertical technology, the company found a way to turn off the elevator’s lights, fan, and even to de-energize its drive: they created a sleeping elevator, so to speak (but one that wakes upon command).
Paradoxically, elevators require energy even when they aren’t in use: when cabs sit idle after the morning rush, for example, elevator systems must be left energized so that they’re ready for the next passenger call. In an effort to reduce wasted energy and improve efficiency, Otis Elevator devised a system called CompassPlus Destination Dispatching, which removes elevators from service when traffic is light. Another device, their patented Gen2 Switch battery-powered elevator, works on solar and wind power, and uses less power than a hairdryer. “Otis technology is now being used daily in over 250 cities across more than 50 countries,” says Tom Vining, president of Otis Americas. “To date, we have sold more than a half-million Gen2 elevators.”
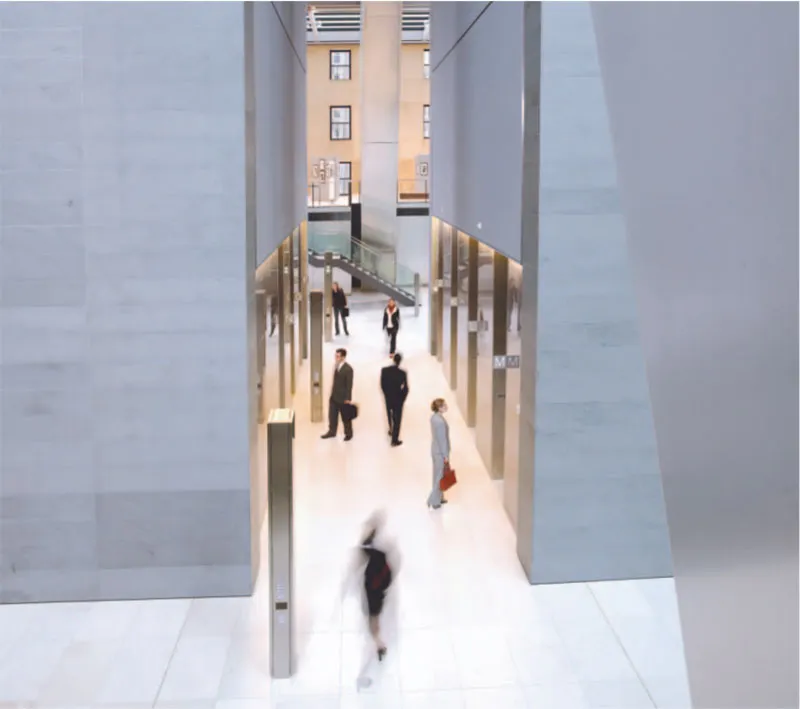
Indeed, Otis is the world’s largest manufacturer of vertical transportation systems, with elevators in some of the world’s most iconic structures, including the Eiffel Tower, the Empire State Building, the original World Trade Center and the Burj Khalifa (which, at 828 meters, is considered the tallest building in the world). Their elevators date back to the middle of the 19th century, though the use of lifting equipment can be traced even further—to Roman antiquity. Cranes, windlasses and capstans (ancient water-raising devices based on a kind of swinging, see-saw design) may well have inspired the use of counterweights in early elevators and hoists.
Modern elevator engineers, however, are faced with a uniquely modern problem: the struggle to eliminate toxic runoff that results when an elevator cab is submerged by tidal floodwater. Mounting climate change means more severe storm surges, which can inundate elevator shafts. When the water drains, it picks up lubricants, which can travel directly into our water supply, threatening aquatic life. In response, Thyssenkrup developed a petroleum substitute—a canola-based, biodegradable fluid.
Schindler Elevator Corporation, for its part, worked to reduce the fuel consumption of its service vehicle fleet through local material sourcing and hub distribution, which reduces overall transport emissions. “Eighty percent of our equipment components are recyclable,” says Mike Ramandanes, senior vice president of new installations for Schindler Elevator. The company has partnered with some of the most well-known green buildings in the U.S., including Hearst Tower, the first building in New York City to receive the LEED Gold certification (it’s since been awarded platinum status).
Installation prices for the tallest buildings can range from $500,000 for single-car elevators to more than $1 million for double-deckers (which stop on alternate floors, reducing the number of stops per run), according to a 2017 global report by Orbis Research. Utility companies do provide limited tax incentives for green “modernized” elevators, and some installers offer on-site metering to show businesses and tenants that the energy savings is real. But capital strategy and the push to sell products is mostly the work of the elevator manufacturers themselves.
While an elevator upgrade is expensive, the dividends are well worth it. And when developers adopt sustainable vertical technology, they spur innovation. An innovation like Thyssenkrupp’s “TWIN,” a double deck elevator with independent cabs that travel on the same guide rails, allows for seamless movement between the top and bottom zones of 30-plus-story buildings—potentially freeing up an entire floor for business or residence. Smaller elevator mechanisms, like those devised by Otis, replace conventional ropes with flat belts, which decreases weight and reduces air resistance and heat friction. These solutions appeal to consumers, but they can also offer building owners significant reductions in energy expenses, and a more elegant aesthetic indoors.
Many companies are testing even newer technology offsite. Helsinki-based elevator manufacturer Kone Oyj, for example, drilled 350 meters into a limestone mine to create a technology lab where it conducts experiments with patented hoisting material, robotics, vibrational resonance and free falls. And in Germany, Thyssenkrupp is testing its new “MULTI,” which relies on magnetic fields instead of cables and can run inside or outside a building, vertically or horizontally, offering architects a new range of possibilities.
But the epicenter of the high-rise frenzy might be Asia and the Middle East. China’s historic urbanization program has dramatically increased the number of vertical transport projects there. In Dubai, home to 18 of the tallest towers in the world, panoramic elevators, ergonomic breaking systems and noise-cancelling technology are hallmarks of a new frontier in vertical technology. Saudi Arabia’s Jeddah Tower will be the first building to reach 1,000 meters—that’s nine times the height of NASA’s first moonshot rocket—when it’s finished in 2020.
The day will come when a passenger can ride up to the 300th story of a cloud-covered tower, her upward journey propelled by rope-less cabs and solar power. Elevators will then be free to journey any which way, Willy Wonka-style, and architects will no longer be limited by the vertical direction of upward travel, or by the constraints of the ground below. On a planet where land resources are finite, sustainable elevation is paramount.
“With immense urbanization at hand,” says Ramandanes, “it is our job to ensure we have the capability to literally go higher than ever before.”