On a narrow, empty lot behind a sign that read “Habitat for Humanity: Live Life in 3D,” Sierra Romas watched as a nozzle on a gantry that moves on rails poured concrete layer by layer—166 in all, each less than an inch high—to build the walls of her three-bedroom house.
“It was amazing, very surreal to see a machine doing everything,” she says on a winter evening, sitting in the living room of the finished home she shares with her two sons.
That surreal 3D-printed home built and sold to Romas in Newport News, Virginia, offers one potential tool to combat the growing affordable housing problem, which the National Low Income Housing Coalition says has grown to a need for more than 7 million homes.
/https://tf-cmsv2-smithsonianmag-media.s3.amazonaws.com/filer_public/7f/9e/7f9e1875-0f4b-438c-b24f-e11e54877414/53513480758_53b68b0716_o.jpg)
Concrete printing is faster—the walls for Sierra’s 1,300-square-foot home were constructed in about 40 hours. It’s also becoming cheaper than conventional wood-frame building, which has changed little in a century.
Romas’ home is the third that the Habitat for Humanity Peninsula and Greater Williamsburg chapter has built. Janet Green, the chapter’s chief executive officer, says each home has been less expensive than the previous. Sierra’s cost Habitat about $215,000, which amounted to $25,000 less than the first one; the land was free from the city’s housing authority. “We suspect the eventual cost to print future 3D homes for Habitat would be around $180,000 to $190,000,” she says. These days, the average listing price for a home that size in Sierra’s area is over $260,000.
Other benefits exist beyond speed and affordability, too. Construction is cleaner, resulting in less waste. (The United States creates 600 million tons of construction and demolition debris annually.) The 3D-printed homes are more energy-efficient because concrete offers better insulation, lowering heating and cooling costs. They’re also far less likely to burn or be blown down, potentially reducing insurance costs. The automation of printing walls and sometimes foundations requires less labor—3D printers can work with only one or two people—at a time when there is a shortage of construction workers.
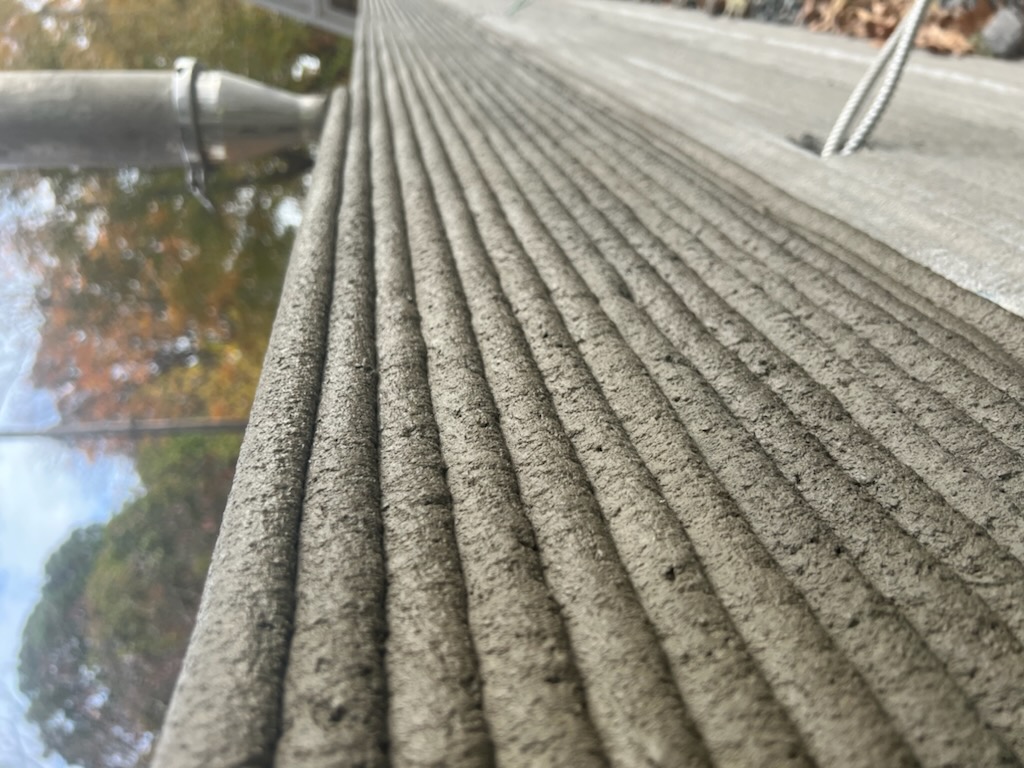
As 3D housing has slowly gained momentum, proponents say it will be a new way to offer people like Sierra, an Army National Guard veteran, homeownership.
Alquist 3D, the company that printed the three Habitat houses, moved its headquarters from Iowa to Greeley, Colorado, last year, enticed by $4 million in incentives from the city and state. There, the outfit plans to build 100 homes as part of a 300-home Habitat for Humanity project. It’s also working with Aims Community College to create a 3D-printing curriculum, training workers who will be needed to grow the technology’s reach.
The biggest entrant into the 3D-building market is Texas-based Icon, which has more than 400 employees. Icon is working with Lennar, the second-largest home builder in the United States, to print 100 houses in a 500-unit development with architecture co-designed by Bjarke Ingels Group outside Austin, Texas, where housing costs have skyrocketed. The median comparably sized Austin-area home lists for over $800,000, but these units are currently priced between $469,990 and $578,990. Exterior and interior walls for each of those printed homes were completed in two weeks and the traditional finishing in about six months. Residents recently moved into the first of the homes sold. “We’re introducing drastic time saving, which of course translates into a huge value add in terms of costs and financing,” says Melodie Yashar, Icon’s vice president for building performance and design.
/https://tf-cmsv2-smithsonianmag-media.s3.amazonaws.com/filer_public/30/95/3095e253-3a23-4b83-92f3-ca654e42ffb0/lennar_icon_3d-printed_100-hmcommunity_wolfranch_conceptrender_aerialnov2022.jpg)
The company, which has also printed military barracks, has ambitious goals. It has raised more than $430 million in financing and landed a $57 million contract with NASA to work on moon habitats. “What if we could build houses that work twice as good, in half the time and at half the price?” Jason Ballard, Icon’s CEO, asked at a conference in 2022. “What kind of problems could we solve? And what kind of opportunities would open up before us?”
Icon printed a community of homes that were granted to people in extreme poverty in Mexico in partnership with New Story, a San Francisco nonprofit building housing in Latin America.
In March, Icon will announce the winners of a global $1 million competition called Initiative 99 to create a design for a 3D-printed house that can be built for $99,000. The company has received hundreds of submissions from 60 countries. To show what’s possible, Icon will build one or more of the winning designs within one of its projects.
“Initiative 99 is a global competition that we’ve hosted to identify key design, both from architecture professionals as well as students, who can really change and shift the discourse to date on affordable housing,” Yashar says.
/https://tf-cmsv2-smithsonianmag-media.s3.amazonaws.com/filer_public/e0/51/e051504c-c1a5-4045-bd4d-4303e054d84d/lennar_icon_3d-printed_100-hmcommunity_wolfranch_printextrusion_in-progress_nov2022.jpg)
The two companies take different approaches. Alquist is a construction firm that buys or leases the printers. Icon is a manufacturer that partners with a construction company. It has a proprietary robotic machine called Vulcan and several concrete mixes called Lavacrete. Icon also supplies software that directs the process of printing architectural designs. Alquist, so far, has only printed straight exterior walls, while Icon has printed curved exterior and interior walls.
The need for housing, especially affordable housing, is overwhelming and has been building for decades. In 2021, more than half of renters in 239 of the nation’s 3,143 counties—high-population areas representing a third of all American renters—were “housing-cost burdened,” meaning they spent more than 30 percent of their income on rent. Building of single-family homes hasn’t grown significantly in years; it dropped by 9 percent in 2023 from 2022. The National Association of Realtors says the United States has had a shortfall of 5.5 million homes over the last 20 years.
The idea of printing homes using concrete has been around for a couple of decades. Its roots go back to William E. Urschel’s “Wall Building Machine,” unveiled in 1941 and patented three years later. The machine operated in a circle around a central arm, depositing concrete poured into a hopper in one layer after another. That idea, though, soon disappeared.
It reappeared and started to gain interest after Berok Khoshnevis, an engineer at the University of Southern California, gave a TED Talk in 2012 championing robotic construction. Khoshnevis had been studying what was called “contour crafting” for more than a decade. He projected the technology would become widespread by 2020 and be used to build high-rises by 2025. (Khoshnevis has since backed away from that projection, telling the New Yorker last year that he didn’t think it would become the industry mainstay.)
/https://tf-cmsv2-smithsonianmag-media.s3.amazonaws.com/filer_public/f5/91/f5917ae0-0764-4078-9dd0-4638532e3b0f/lennar_icon_3d-printed_100-hmcommunity_wolfranch_rune_model_home_exterior-2_july2023.jpg)
Icon was founded in 2017 and Alquist in 2020 by men with a passion and a vision that 3D printing promised the answer to what had become a seemingly intractable problem. Ballard, an Icon co-founder, worked at a homeless shelter after college, then started a sustainable building supply business in Austin. When he searched for something that would more radically disrupt the building industry, 3D printing won his heart.
Zachary Mannheimer, the founder of Alquist, was a theater major in college and ran companies doing political theater in Brooklyn, New York. He dreamed of inspiring people with opposing views, but he found most of his Brooklyn neighbors agreed with him—so he moved to Des Moines, creating a cultural center, the Des Moines Social Club, and then branching out to work on creative placemaking and economic development in smaller communities throughout the Midwest.
“But everywhere we went, the No. 1 issue every year was housing,” he says. “It didn’t matter if we created a cool theater or cultural center, or even found them funding for child care. If they didn’t have anywhere to live, none of that really mattered. So we started exploring ways to solve the housing problem. In 2016, I discovered 3D-printed homes and got obsessed with it.”
Both Icon’s Yashar and Alquist’s Mannheimer are clear that the technology faces hurdles. “People really wanted to get into the 3D world to save money versus traditional builds,” Mannheimer says. “We believe it will in time. Right now, it’s not saving anything dramatic.”
The key to lowering costs is scaling up construction on a site. “3D printing is about 10 to 30 percent cheaper to build, as compared with traditional means and methods of construction,” Yashar says, adding that the savings mount the more you build on a site. The time saving— printing walls in only two weeks—also translates to a value-added in terms of financing.
“By taking advantage of the cost optimization and time optimization of this technology, we can actually make a dent in what we believe is a global housing crisis,” she adds.
/https://tf-cmsv2-smithsonianmag-media.s3.amazonaws.com/filer_public/20/ac/20acc70d-055f-4f9e-b3ab-b9e697c0c07a/lennar_icon_3d-printed_100-hmcommunity_wolfranch_rune_model_home_patio_july2023.jpg)
To make the technology more robust and attractive, Icon has a research and design arm that is working on different systems to print in different climates, as well as a program testing wall resiliency against tornadoes, hurricanes and storms, Yashar says.
Mannheimer also says the cost of the concrete material needs to fall for the savings to rise. “We have to drop that and localize the material, as well as make it greener, and more friendly for the environment,” he adds. And thousands of workers need to be trained in the technology, though 3D printing only requires one or two people on site.
“We’ve only been 3D printing in America for about five years. It’s still very new. Nobody’s doing it perfectly,” Mannheimer says. “It’s a constant learning process every time we do this. I suspect that won’t change for probably the next 20 years.”
Andrew McCoy, director of the Virginia Center for Housing Research at Virginia Tech, got involved with the three Habitat homes in Virginia after publishing a study showing the state needed 275,000 new homes but was only building 20,000 a year. The university is working with Habitat to monitor the energy efficiency of the homes, and, so far, they are exceeding expectations.
McCoy says market conditions present an opportunity for 3D printing. “We’re in a unique position where borrowing money is expensive right now. We have a hard time finding labor. And when we do, we have to train them and get them up to speed,” he says. “Material costs are really high. The length of time from when we start work to when we get a client into a building has expanded. All these things lend nicely toward a technology like this.”
McCoy notes the building industry needs to be convinced to change the way it’s been raising homes for more than a century. Rather than present construction companies with a concrete printer as an end solution, he wants to engage them in the development of the product to match their needs. “They know the path that got them here,” he explains. “It’s been successful so far—why change that up? So, we want to get in there and say, ‘Look, let’s put this in front of you. How would you use it? How would you like to work with it?’”
Ask proponents when the process will become widespread and the answer is years, anywhere from 2 to 20. McCoy says the Icon project in Texas with Lennar could show builders this is the way. But he’s also not convinced 3D concrete printing is the future. That future might be a combination, including 3D metal and plastic printing of building components that will also save time and money and be easier to access.
The present technology—lumber-framed homes—has evolved over more than a century. Give 3D printing time, McCoy says. “For some reason, we want these things to work out of the box and make money for everybody instantly, and it just doesn’t work that way,” he adds.
/https://tf-cmsv2-smithsonianmag-media.s3.amazonaws.com/filer_public/b9/df/b9df5052-aa10-45fa-ac2e-00b9bb16ef92/2_icon_olympus_multi-purpose_isru-based_lunarconstructionsystem_habitat_concept-render_nov2022.png)
One company that is exploring printing home components is Mighty Buildings, which has a $5 million grant with the Lawrence Berkeley National Laboratory and Habitat for Humanity to develop sustainable and affordable housing in the San Francisco Bay Area. It is also building net-zero energy homes in a couple of California communities. The company, which has raised $150 million in funding, supplies a kit of 3D-printed wall panels, doors, windows and roof sections that can be assembled in four days.
“A big benefit for developers is that we shrink the time they need to pay interest on construction loans,” says Alexey Dubov, one of the company’s founders. Its process also addresses the climate crisis. Mighty Buildings’ synthetic stone material uses recycled glass, and the highly insulated homes it builds, with solar panels on their roofs, mean they may produce as much energy as they use.
Will 3D printing for construction gain wide acceptance? Mannheimer is cautiously optimistic.
“There’s two answers to solving this problem of housing. One is: Companies should pay their employees more to afford the rising costs, which, of course, we have no control over,” he says. “Or we have to lower the cost of the materials in the process. Or ideally both. That’s the only solution. So, I think 3D is going to get us there in the next couple of years. But there’s a lot more trial and error that we need to go through.”