An Aerial Food Drop Over Syria Missed Its Target, and That’s No Surprise
An experienced C-130 officer explains why it’s so hard to get drops right from high altitudes.
/https://tf-cmsv2-smithsonianmag-media.s3.amazonaws.com/filer/45/08/45084ee5-f1cf-486c-8cf7-8346791726de/36th_airlift_squadron_c-130_osakabe_yasuo.jpg)
Two weeks ago, the United Nations World Food Programme’s attempt to air-drop 21 pallets of food to some 200,000 starving Syrians in the ISIS-beseiged city of Deir ez-Zor ended in failure. The threat of anti-aircraft fire forced the Russian transport aircraft chartered by the U.N. to release its cargo—enough lentils, rice, vegetable oil, and salt to feed 2,500 people for a month, the food agency said—from an altitude of 23,000 feet. The Guardian reported that four pallets were destroyed because their parachutes didn’t open, seven landed too far away from the target area to be of benefit, and 10 had drifted so far off course they could not be located.
Unfortunately, that’s not a surprise, according to a U.S. Air Force officer with substantial experience in humanitarian airdrops. The officer, a former C-130 squadron commander, spoke to Air & Space on the condition of anonymity, as he had not been authorized to comment. (For simplicity’s sake, we’ll call him Al.)
Al says that air drops are C-130 crews’ most important function. The higher up you go, the more difficult it is to deliver a payload intact and on-target. “There are very few nations that air-drop,” he says, “and the U.S. is the only one that does it writ large.” He’s skeptical that private charter operations would have the expertise or the equipment to do it effectively.
“Very few other entities or commercial carriers or charter carriers do it, and if they do, it’s pretty much, ‘You rig it up, we’ll push it out the back.’ But there’s a lot of expertise in the very boring part of it: How [the cargo] is rigged, the type of parachutes used.” Rigging, he notes, has its own Air Force Specialty Code. “You go to rigging school.”
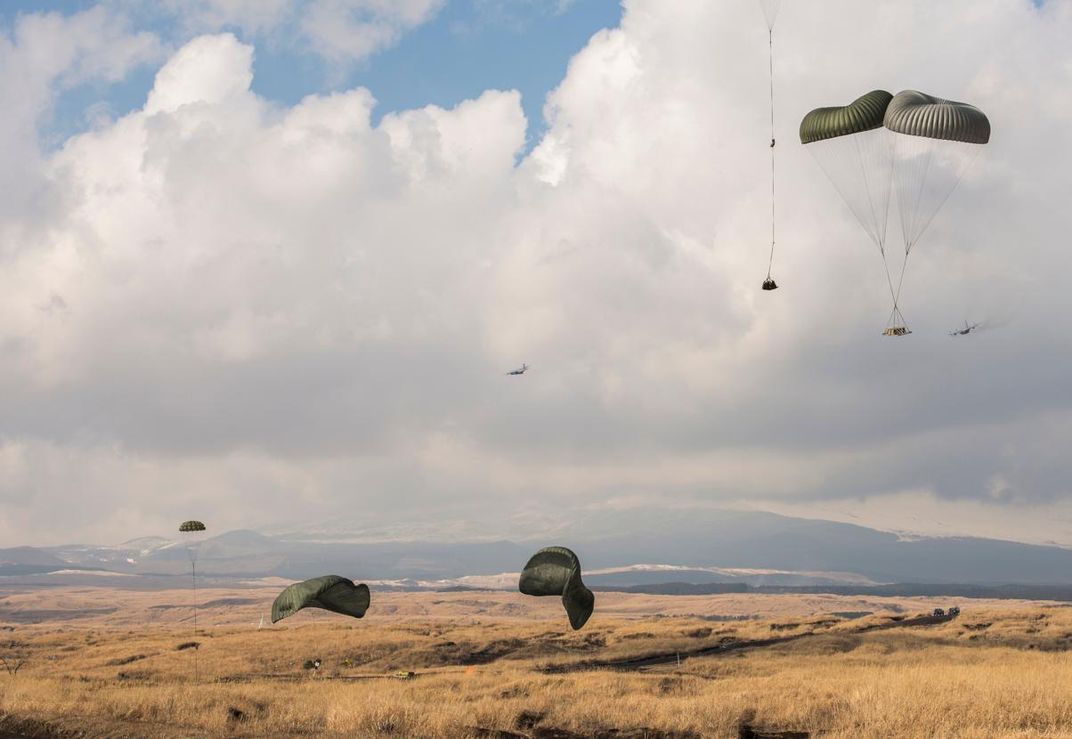
The forces acting on a parachute attached to an object pushed out of an airplane traveling at 120 knots are dramatic. “Opening shock can be 18 to 21 Gs,” he says. “So your 100-pound box just became a 2,000-pound box. And the tensile strength of your webbing changes when it bends. It’s all just high school physics, but if you’re a charter enterprise, and you don’t have the expertise behind you, it’s pretty hard.” He says the tiny details that less experienced crews are prone to overlook can make the difference between success and failure. For example, webbing that isn’t arranged just-so can be damaged as it travels over rollers on its way out of the cargo bay, which makes it more susceptible to breakage, especially during the shock of chute inflation.
“Murphy lives all over this process,” says Al.
For high-altitude, high-accuracy drops, the U.S. military uses a technology known as the Joint Precision Airdrop System (JPADS), which has been deployed for only about a decade. The system includes a dropsonde, a sort of probe that’s dropped prior to the cargo to take readings of wind speed and direction, which it sends to the mission planning software. That data helps planners determine their Computed Air Release Point, or CARP. Once the payload is dropped, onboard actuators and a steerable parafoil canopy help guide the pallet to its target. That’s critical, Al says, because a pallet dropped from 20,000 feet will take five or six minutes to reach the ground, and will be subject to wind that entire time. “It’s always windy up high,” Al says. JPADS systems cost about $60,000 apiece and usually must be recovered on the ground after a drop. “You wouldn’t use it for a purely humanitarian drop.”
He says that the Improved Containerized Delivery System would be ideal for the conditions like the ones the U.N. is facing in Syria. As with JPAD drops, a dropsonde is released 15 to 20 minutes prior to the payload drop, from a point within 30 kilometers (19 miles) of the drop zone to help determine the CARP.
At lower altitudes, there’s a lot less that can go wrong. Al says that in a “permissive environment,” where the aircraft is not at risk of being shot down, the most reliable method is a Containerized Delivery System—a 2,000-pound bundle about three-quarters of the size of a standard refrigerator, typically dropped from 500 feet. There’s also the Low Cost Air Drop System, which gets dropped from 300 feet. “That one is a 600-pound box,” Al says. “It’s only under ’chute for five seconds, so there’s not much risk of drift, no matter how fast the wind is.”
In Bosnia in the ’90s, Al says, U.S. forces would sometimes send an A-10 Warthog up to 20,000 feet to take wind readings in advance of an airdrop. Absent the sophisticated software that would become available in the 21st century, the navigator would have to calculate the release point by doing “a whole bunch of math on his whiz wheel,” referring to the circular analog flight computers that remain in use today. “Not that much differently than they would’ve done it in 1945.”
He says that without accurate wind information, putting a payload on target from high altitudes is virtually impossible.