NASA’s New, Super-Efficient Airplane Wing Comes With a Twist
The agency and several universities have designed a flexible wing that could reduce the cost of building and fueling airplanes
/https://tf-cmsv2-smithsonianmag-media.s3.amazonaws.com/filer/3b/01/3b01463d-007c-4eaf-ac0d-5f215b2d6f14/mit-bendingwings-2-press.jpg)
Ailerons, rudders, wing flaps—all those things that keep a plane going straight, or allow it to chart a new course—were only ever an approximation. Normally, these pieces attach to the back of the wing and the tail, and when they move up or down, create drag and cause the plane to change directions or altitude.
A continuous, flexible wing built by NASA and collaborators at MIT, University of California, Santa Cruz, and several other universities could achieve the same result more efficiently, cutting both fuel consumption and the cost of building the planes.
“One of the main points is that we can get this kind of performance at an extremely low cost,” says Kenneth Cheung, a NASA scientist who is co-lead on the project. “And there’s this promise of scalability out of the fact that we can use relatively small building blocks.”
The wing, described in the journal Soft Robotics, is made up of small carbon fiber parts that intersect to form a flexible, lightweight lattice that’s still stiff in all the right directions.
The drag on a traditional wing induces a sort of eddying current of air around the wing (more than is needed for lift alone) and that air vibrates with what are called flutter modes, the shape and size and frequency of which depend on the speed of the craft. A stiff, heavy wing like the aluminum one on a 747 is strong enough to withstand that vibration and not shear off, even at high speeds. This is a model airplanes have reached based on decades pursuing faster flight, says Cheung.
The upshot is, all around a plane in flight are moving shapes made of air. Cheung calls them the free stream, and his goal is to match the shape of the plane, at any given moment, to the stream. A twist in the wing can make the plane change shape smoothly, a little like a surfer catching a wave.
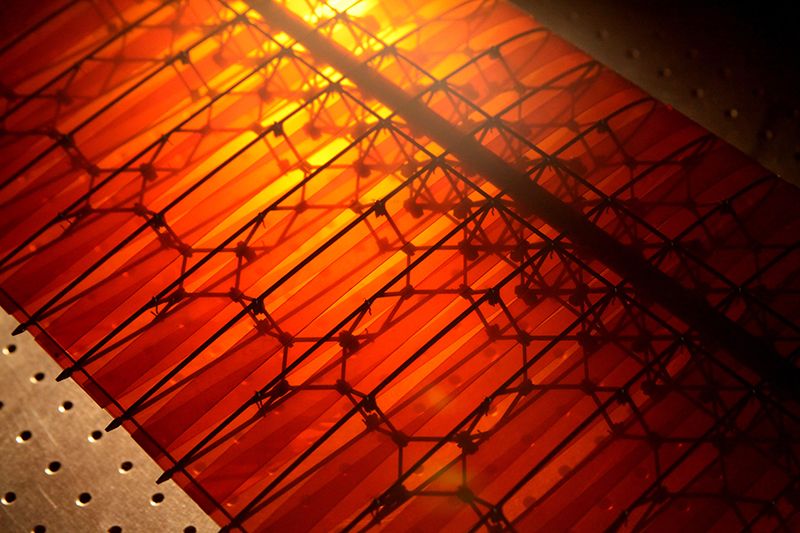
“The rigid ailerons are just a loose approximation of what is really the condition that you are trying to achieve,” he says. “So the efficiency gains that you get by actually matching the aerodynamic condition can be really significant.”
It’s no new thing to build a wing that can change shape. In fact, the Wright Brothers did it—their aircraft was based on flexible wood and canvas wings. More recently, Airbus has experimented with flexible 3D printed wings, and a company called FlexSys published video this month of a more traditional aileron that flexes instead of slides.
“It’s a pretty major efficiency improvement in an aircraft,” says David Hornick, president and COO of FlexSys. “You’re actually maintaining a true airfoil shape when you’re doing this morphing approach. The airfoil shape is still there, you’re reducing the amount of drag that would be created by putting a hinged control surface on it.”
“The fully flexible wing will be a little bit challenging” because it’s less similar to traditional wing shapes, Hornick says. “But quite honestly, what they’re doing is pretty remarkable.”
Other researchers at the Delft University of Technology and at Texas A&M have also designed and built morphing wings, but what’s special about NASA’s wing is inside it. Carbon fiber is light, moldable, and stiff. But it is brittle, and prone to breaking when stressed in the wrong direction. Cheung and his team developed a small, interlocking unit that can be pieced together to make a three-dimensional lattice of carbon fiber. Individually, they are stiff, but the whole is flexible. It’s also extremely light.
“If you take this building block strategy to building these three-dimensional lattices out of carbon fiber parts, you get something you can treat as a continuous material,” says Cheung. “You get incredibly good performance. We actually showed the highest specific stiffness ever shown for an ultra light material.”
Once the lattice was built, the team ran a rod from the fuselage to the wing tip, which, when rotated by a motor in the body of the plane, twists the tip, and the rest of the wing follows. The whole thing is sheathed in a polyimide called Kapton, a coppery, tape-like material used in flexible circuit boards.
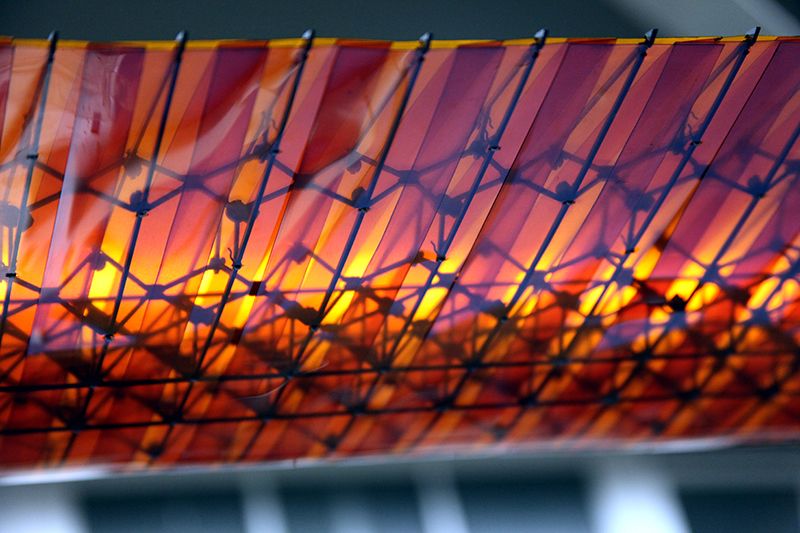
A further benefit is the modularity of the components; nearly the entire wing was assembled from identical pieces, meaning an airline that wanted to use them could save big on the manufacturing process as well. They could also be replaced individually, meaning cheaper repairs, or reconfigured into new shapes for other aircraft.
“What they’ve done is, they’ve used these light, stiff structures in a way that makes the whole structure deformable,” says Haydn Wadley, a professor of materials science and engineering who works on deformable, but strong lattices of shape-memory alloys at the University of Virginia. “This is the kind of thing, you could imagine a wind turbine that changes the shape of an airfoil to determine the amount of energy it sucks out of the wind.”
The research team has already mounted the wing on a remote-control airplane, and future test flights will feature bigger planes—up to three-meter wingspan—with sensors mounted on them to monitor the wing and how well it matches the air stream around it. Eventually, the technology could appear in manned aircraft or even commercial airplanes. But even the sky might not be the limit.
“We’re looking forward to potential space applications as well. Obviously, if you’re going to build a spaceship or a habitat in space, you don’t have a factory there to build it,” says Cheung. “We know we have all of these applications in space that are much larger than we can launch, so we have to build them.”